A Step-by-Step Guide to Product Structure Design for Optimal Manufacturing
Understanding Product Structure Design
Product structure design is a critical aspect of manufacturing that ensures efficiency in production processes. It involves organizing all the components of a product in a way that optimizes assembly, reduces costs, and enhances performance. A well-designed product structure can lead to significant improvements in the production cycle and overall product quality.
In today's competitive market, achieving optimal manufacturing requires a strategic approach to product structure design. This involves a detailed analysis of each component, their interactions, and how they contribute to the final product. Understanding these elements is essential for any manufacturer looking to improve operational efficiency.

Step 1: Define Product Requirements
The first step in designing an optimal product structure is to clearly define the product requirements. This includes understanding the customer needs, regulatory standards, and the intended use of the product. By establishing these parameters, manufacturers can ensure that all design efforts are aligned with the end goals.
Gather input from cross-functional teams, including sales, marketing, and engineering, to ensure a comprehensive understanding of the product specifications. This collaboration helps identify potential challenges early in the design process and enables teams to address them proactively.
Step 2: Develop a Component List
Once the product requirements are defined, the next step is to develop a detailed list of components. This list should include every part required for manufacturing the product, from raw materials to finished components. Organizing these elements into a structured list provides a clear overview of what is needed for production.
Utilize tools like Bill of Materials (BOM) to document and manage the component list effectively. A well-organized BOM ensures that all stakeholders have access to accurate information, facilitating smooth communication and coordination across departments.
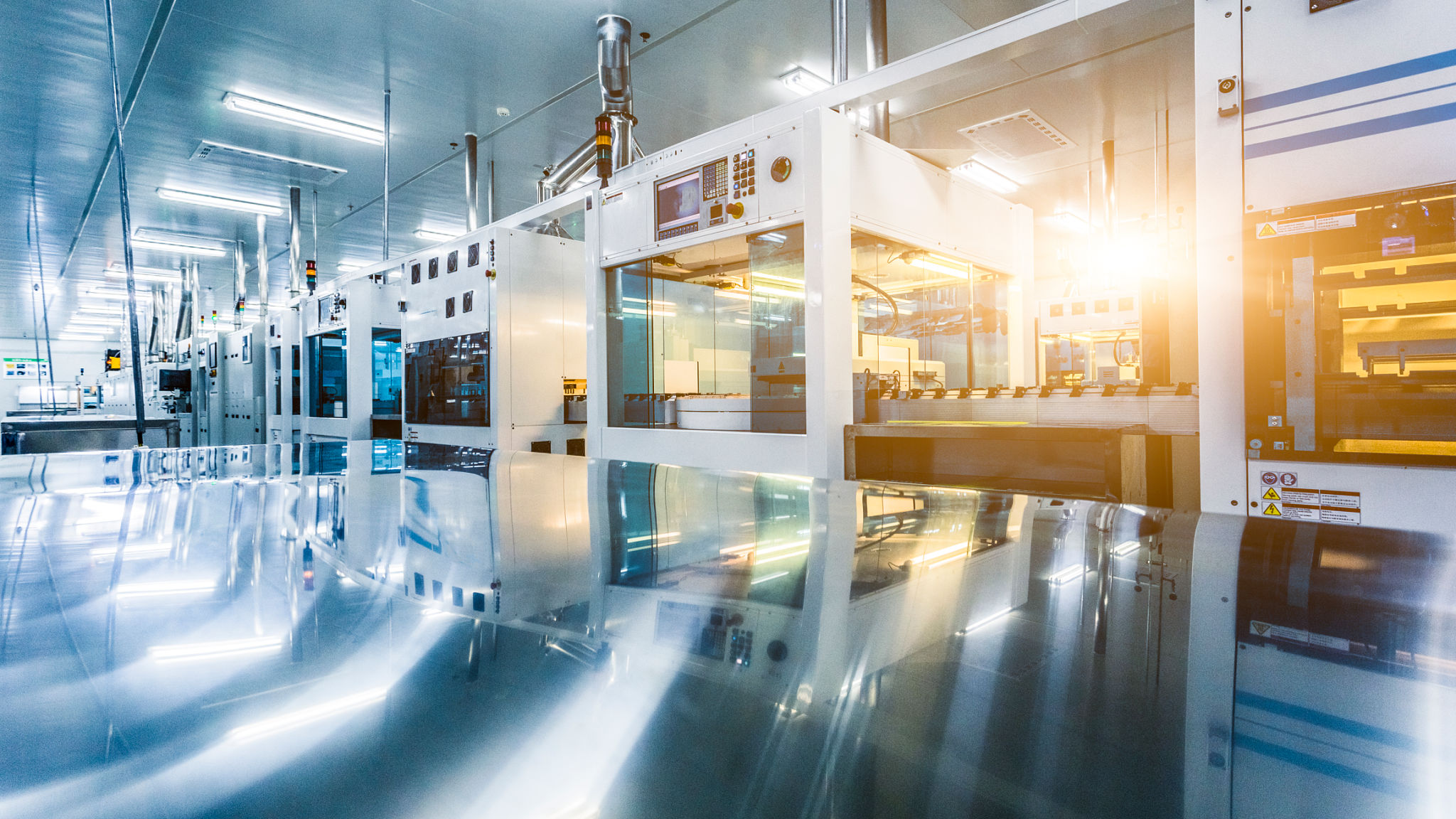
Step 3: Design for Manufacturability
Designing for manufacturability (DFM) is a critical consideration in product structure design. DFM focuses on simplifying product designs to make them easier and cheaper to manufacture. This involves analyzing each component to identify opportunities for reducing complexity, minimizing part counts, and improving assembly processes.
Collaborate with manufacturing engineers to evaluate design options and implement changes that streamline production. This collaborative approach can lead to innovative solutions that enhance product quality while reducing manufacturing costs.
Step 4: Prototype and Test
Prototyping is an essential step in the product structure design process. Creating a prototype allows manufacturers to test and validate design concepts before committing to full-scale production. Through prototyping, teams can identify design flaws and make necessary adjustments to improve functionality and performance.
Conduct thorough testing of the prototype under various conditions to ensure it meets all requirements and performs as expected. This iterative process helps refine the product design, ensuring it is robust and reliable before entering mass production.
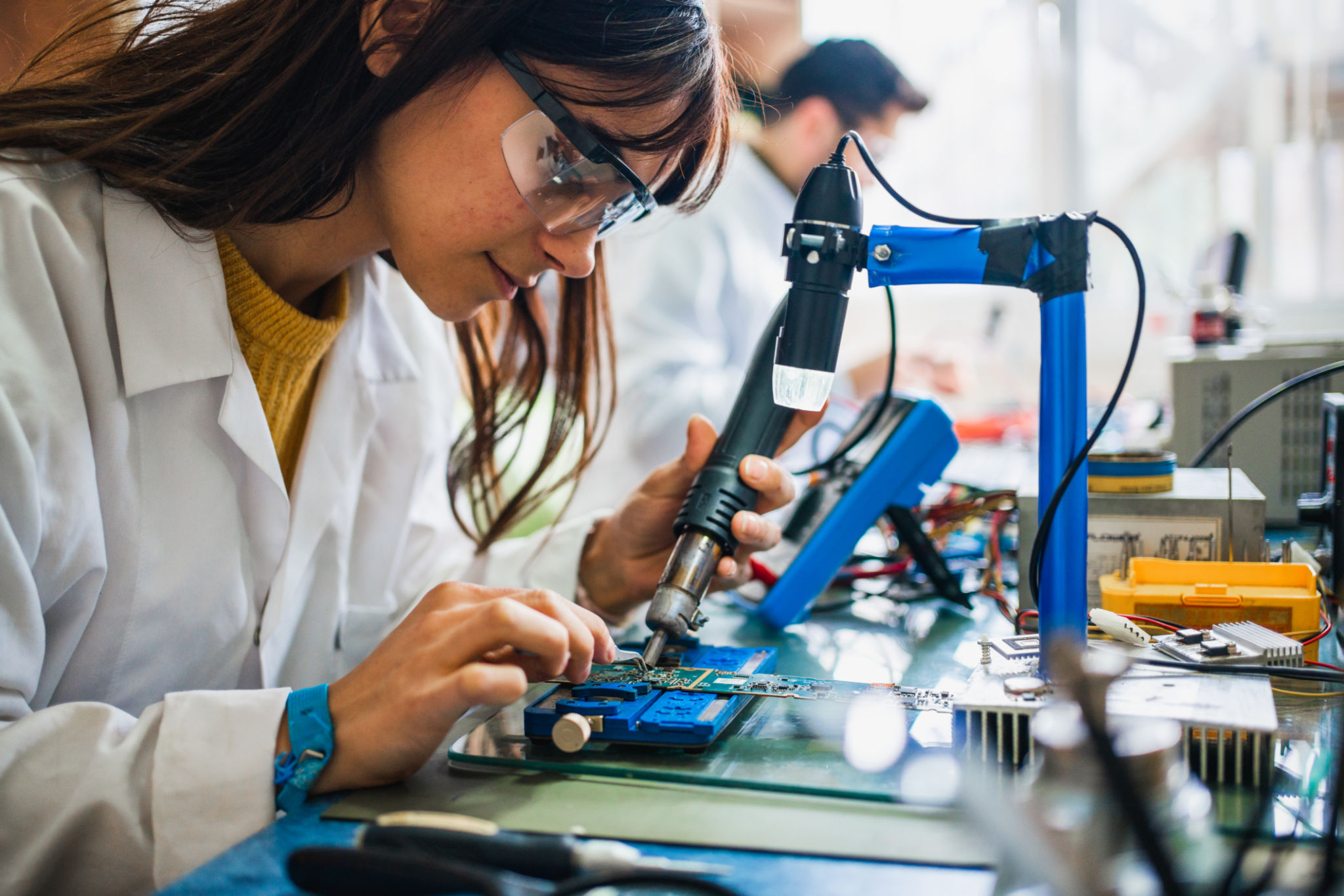
Step 5: Optimize Supply Chain Integration
The final step in achieving optimal product structure design is integrating it with the supply chain. This involves coordinating with suppliers to ensure timely delivery of components and materials. Efficient supply chain management helps minimize lead times and reduces the risk of production delays.
Leverage technology solutions like ERP systems to manage supply chain activities effectively. These systems provide real-time visibility into inventory levels and supplier performance, enabling manufacturers to make informed decisions that support seamless production operations.
By following these steps, manufacturers can create a product structure that supports efficient manufacturing processes, enhances product quality, and meets customer expectations. With careful planning and execution, optimal product structure design becomes an integral part of successful manufacturing operations.